Plastic extrusion for detailed profiles and custom designs
Plastic extrusion for detailed profiles and custom designs
Blog Article
A Comprehensive Guide to the Process and Benefits of Plastic Extrusion
In the vast realm of manufacturing, plastic extrusion emerges as a important and very reliable process. Altering raw plastic into continuous profiles, it caters to a myriad of markets with its exceptional versatility. This overview aims to elucidate the elaborate steps involved in this technique, the kinds of plastic proper for extrusion, and the game-changing benefits it brings to the market. The ensuing discussion promises to unfold the real-world impacts of this transformative process.
Comprehending the Basics of Plastic Extrusion
While it may show up facility initially look, the process of plastic extrusion is essentially simple - plastic extrusion. It is a high-volume production technique in which raw plastic is thawed and formed into a continual account. The procedure begins with the feeding of plastic material, in the type of granules, powders, or pellets, into a warmed barrel. The plastic is after that thawed making use of a mix of warm and shear, used by a turning screw. Once the molten plastic gets to the end of the barrel, it is forced through a tiny opening called a die, forming it into a desired type. The shaped plastic is after that cooled down, solidified, and cut right into desired sizes, finishing the process.
The Technical Process of Plastic Extrusion Explained

Kinds Of Plastic Suitable for Extrusion
The choice of the appropriate kind of plastic is a crucial facet of the extrusion process. Different plastics use one-of-a-kind homes, making them extra matched to specific applications. Understanding these plastic kinds can considerably enhance the extrusion procedure.
Contrasting Plastic Extrusion to Other Plastic Forming Approaches
Comprehending the types of plastic ideal for extrusion leads the means for a wider discussion on just how plastic extrusion piles up against various other plastic creating methods. Plastic extrusion is unrivaled when it comes to producing constant accounts, such as seals, pipelines, and gaskets. It likewise enables for a constant cross-section along the size of the product.
Key Benefits of Plastic Extrusion in Production
In the world of manufacturing, plastic extrusion supplies several considerable benefits. One notable benefit is the cost-effectiveness of the procedure, that makes it a financially appealing production technique. In addition, this strategy offers superior item versatility and improved production rate, consequently boosting general manufacturing efficiency.
Cost-Effective Production Approach
Plastic extrusion leaps to the leading edge as a cost-efficient production technique in production. This procedure attracts attention click reference for its ability to produce high volumes of material promptly and efficiently, supplying suppliers with considerable cost savings. The main cost advantage is the capability to make use of cheaper raw products. Extrusion utilizes thermoplastic materials, which are less pricey compared to steels or porcelains. Additionally, the extrusion process itself is relatively simple, minimizing labor prices. Furthermore, plastic extrusion calls for less energy than standard manufacturing techniques, adding to reduced operational expenses. The process also lessens waste, as any excess or defective materials can be reused and reused, giving an additional layer of cost-effectiveness. Overall, the monetary benefits make plastic extrusion a highly eye-catching choice More about the author in the manufacturing market.
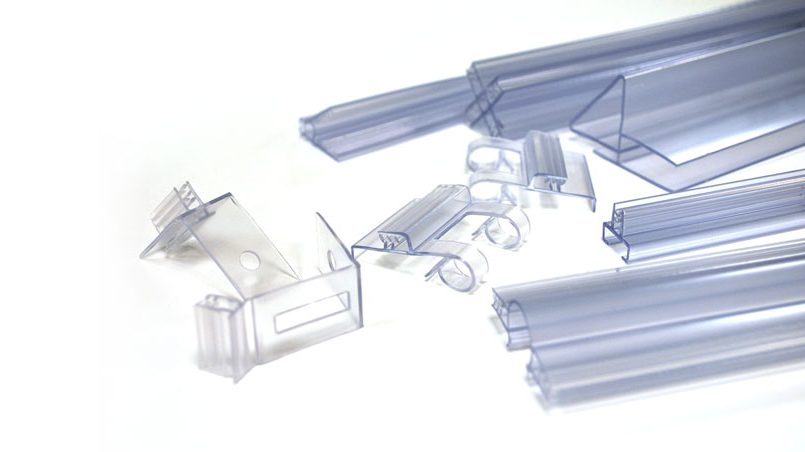
Superior Item Versatility
Past the cost-effectiveness of plastic extrusion, another substantial benefit in manufacturing depend on its superior product versatility. This process permits for the production of a vast array of items with differing sizes, shapes, and styles, from straightforward plastic sheets to intricate accounts. The versatility is credited to the extrusion die, which can be personalized to produce the preferred product layout. This makes plastic extrusion an ideal solution for industries that need tailored plastic components, such as auto, construction, and product packaging. The capacity to produce diverse products is not just helpful in conference details market needs but also in enabling suppliers to discover new line of product with minimal capital expense. In significance, plastic extrusion's item adaptability promotes innovation while boosting operational effectiveness.
Improved Production Rate
A substantial benefit of plastic extrusion lies in its improved manufacturing speed. Few other production procedures can match the speed of plastic extrusion. Furthermore, the capability to keep consistent high-speed manufacturing without giving up product top quality establishes plastic extrusion apart from other methods.
Real-world Applications and Effects of Plastic Extrusion
In the realm of manufacturing, the method of plastic extrusion holds extensive importance. This process is commonly utilized in the production of a variety of products, such as plastic tubes, window structures, and climate navigate to this website stripping. Therefore, it greatly affects markets like construction, packaging, and automobile markets. Its influence extends to daily items, from plastic bags to tooth brushes and non reusable cutlery. The financial benefit of plastic extrusion, mainly its economical and high-volume result, has actually revolutionized manufacturing. Nonetheless, the ecological impact of plastic waste continues to be a worry. Consequently, the market is persistently making every effort for advancements in recyclable and eco-friendly products, showing a future where the advantages of plastic extrusion can be kept without compromising ecological sustainability.
Final thought
Finally, plastic extrusion is a effective and extremely effective approach of transforming raw materials into varied items. It supplies countless benefits over other plastic forming techniques, consisting of cost-effectiveness, high output, minimal waste, and design versatility. Its impact is profoundly really felt in numerous industries such as building and construction, vehicle, and consumer goods, making it a critical procedure in today's manufacturing landscape.
Digging deeper into the technological procedure of plastic extrusion, it begins with the choice of the suitable plastic product. Once cooled down, the plastic is cut right into the needed sizes or injury onto reels if the item is a plastic movie or sheet - plastic extrusion. Contrasting Plastic Extrusion to Various Other Plastic Forming Methods
Comprehending the kinds of plastic suitable for extrusion leads the means for a broader conversation on just how plastic extrusion piles up versus other plastic developing methods. Few various other manufacturing processes can match the rate of plastic extrusion.
Report this page